support@comsol.com
Nonlinear Structural Materials Module Updates
For users of the Nonlinear Structural Materials Module, COMSOL Multiphysics® version 6.2 provides new functionality for parameter estimation, new material models for polymer viscoplasticity, and an update to the kinematic hardening model that enables it to handle large plastic strains. Read more about the updates below.Parameter Estimation
In this version, enhanced parameter estimation capabilities have been introduced, including improvements to the Levenberg–Marquardt and interior point optimizer (IPOPT) solvers. These additions can significantly enhance the performance of parameter estimation of experimental data, including uniaxial, biaxial, and cyclic load cases. Three new tutorial models in the Application Gallery demonstrate this new functionality:
- parameter_estimation_hyperelasticity
- parameter_estimation_plasticity
- parameter_estimation_polymer_viscoplasticity
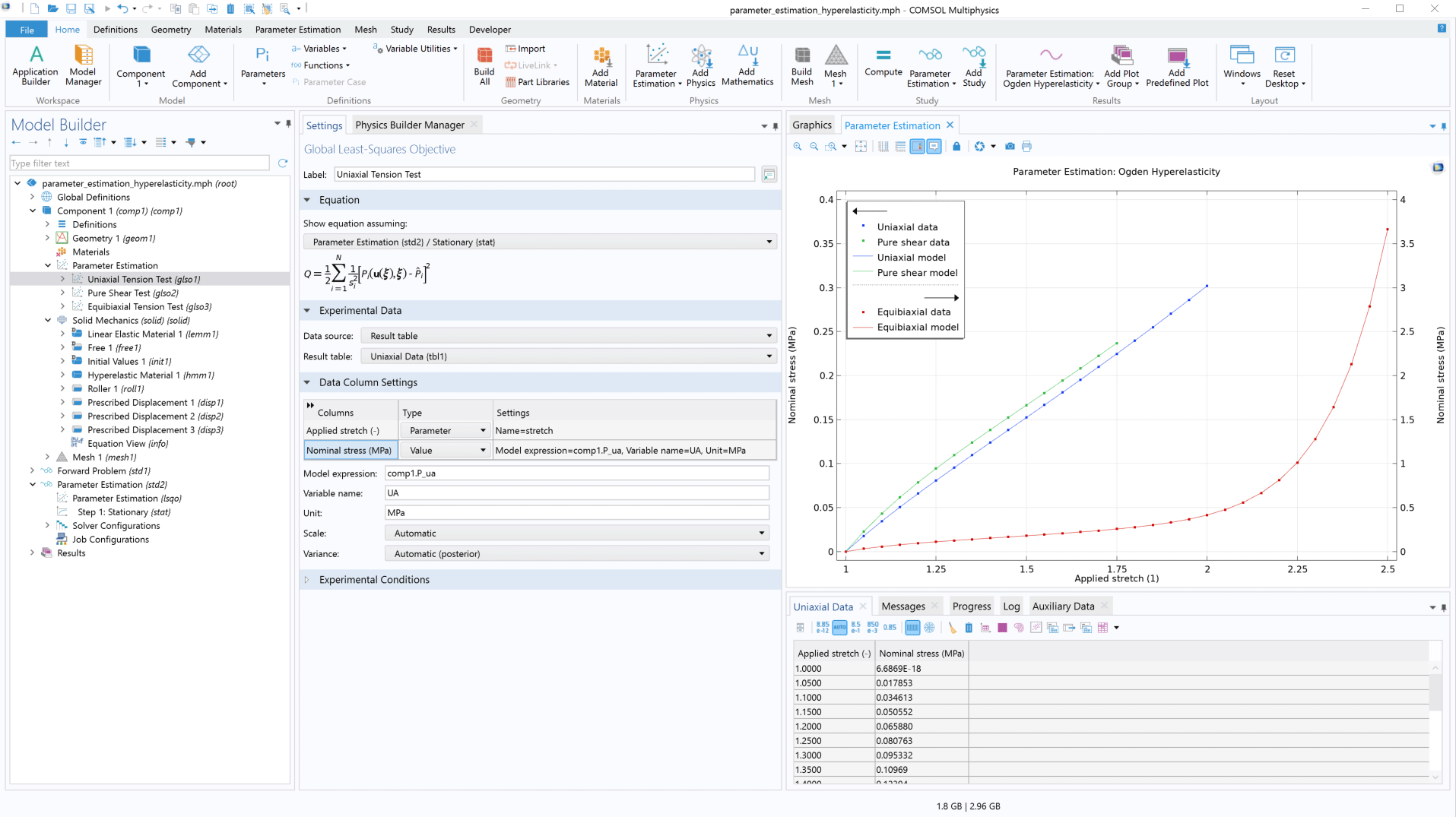
Polymer Viscoplasticity
In order to accurately analyze structures made of solid polymer materials, new material models for polymer viscoplasticity have been added. These include the Bergstrom–Boyce, Bergstrom–Bischoff, and parallel network models. This new framework can handle large viscoplastic strains, and it is based on the multiplicative decomposition of deformation gradients. You can see these new additions in the following tutorial models:
- chloroprene_rubber_compression_test
- buckling_hdpe_linear
- small_punch_test
- parameter_estimation_polymer_viscoplasticity
Fiber Enhancements
Version 6.2 introduces several improvements to the Fiber feature, including:
- Compressible fibers within the Holzapfel–Gasser–Ogden hyperelastic material model
- The Thermal Expansion feature for fibers embedded in hyperelastic materials
- The Uniaxial data material model for handling nonlinear stress–strain relationships for fibers within the Linear Elastic Material and Nonlinear Elastic Material features
These new improvements can be seen in the new Tire Inflation tutorial model.
Shape Memory Alloy Enhancements
The updates for shape memory alloys include:
- Enhanced flexibility in specifying material parameters for phase transformation, allowing inputs to be entered as start and finish stresses or start and finish temperatures
- Introduction of a new predefined plot showing the stress–temperature phase diagram, which illustrates the austenite-to-martensite transition
- Significantly improved penalty method for enforcing upper bounds on transformation strains
- Inclusion of the Prager–Lode yield surface, enabling the modeling of anisotropic deformation for tension or compression
- Introduction of large-strain plasticity capabilities
You can see these enhancements in the new Uniaxial Loading of Shape Memory Alloy Using Souza–Auricchio Model tutorial model.

Viscoplastic Material Model for Lithium
A new material model, Anand–Narayan, has been added to the Viscoplasticity feature. This material model specifically targets the properties of lithium in battery applications.

New Phase-Field Damage Multiphysics Interface
The new Phase-Field Damage multiphysics interface combines a Solid Mechanics interface with the new Phase-Field in Solids interface through a Phase-Field Damage bidirectional multiphysics coupling. The stress or the strain energy density drives the evolution of the phase field, and the phase field determines the degree of damage to the elastic material model.
New Tutorial Models
COMSOL Multiphysics® version 6.2 brings several new tutorial models to the Nonlinear Structural Materials Module.
Large Swelling in Polymer Hydrogels
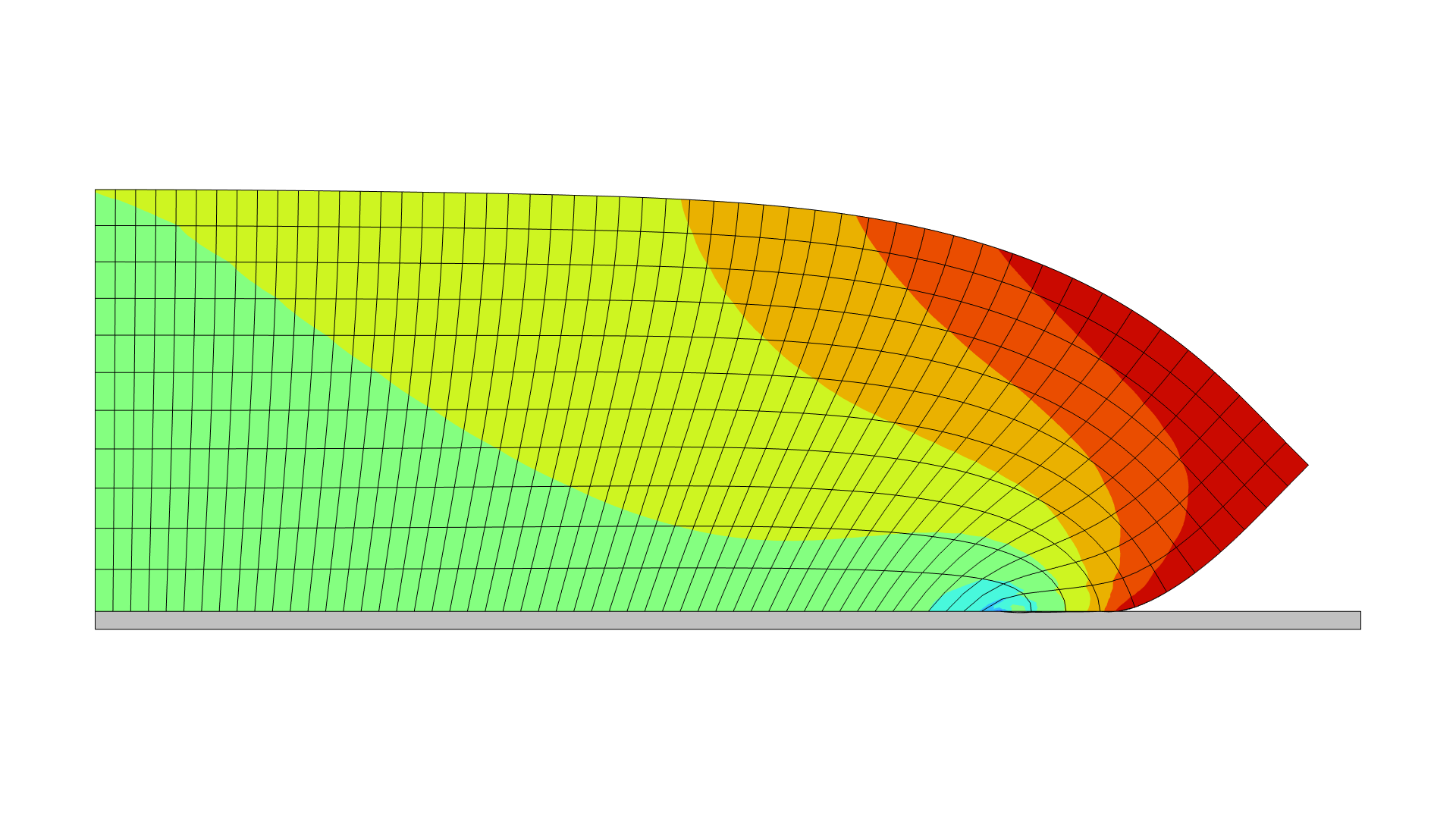
Application Library Title:
hydrogel_swelling
Download from the Application Gallery
Uniaxial Loading of a Shape Memory Alloy Using the Souza–Auricchio Model
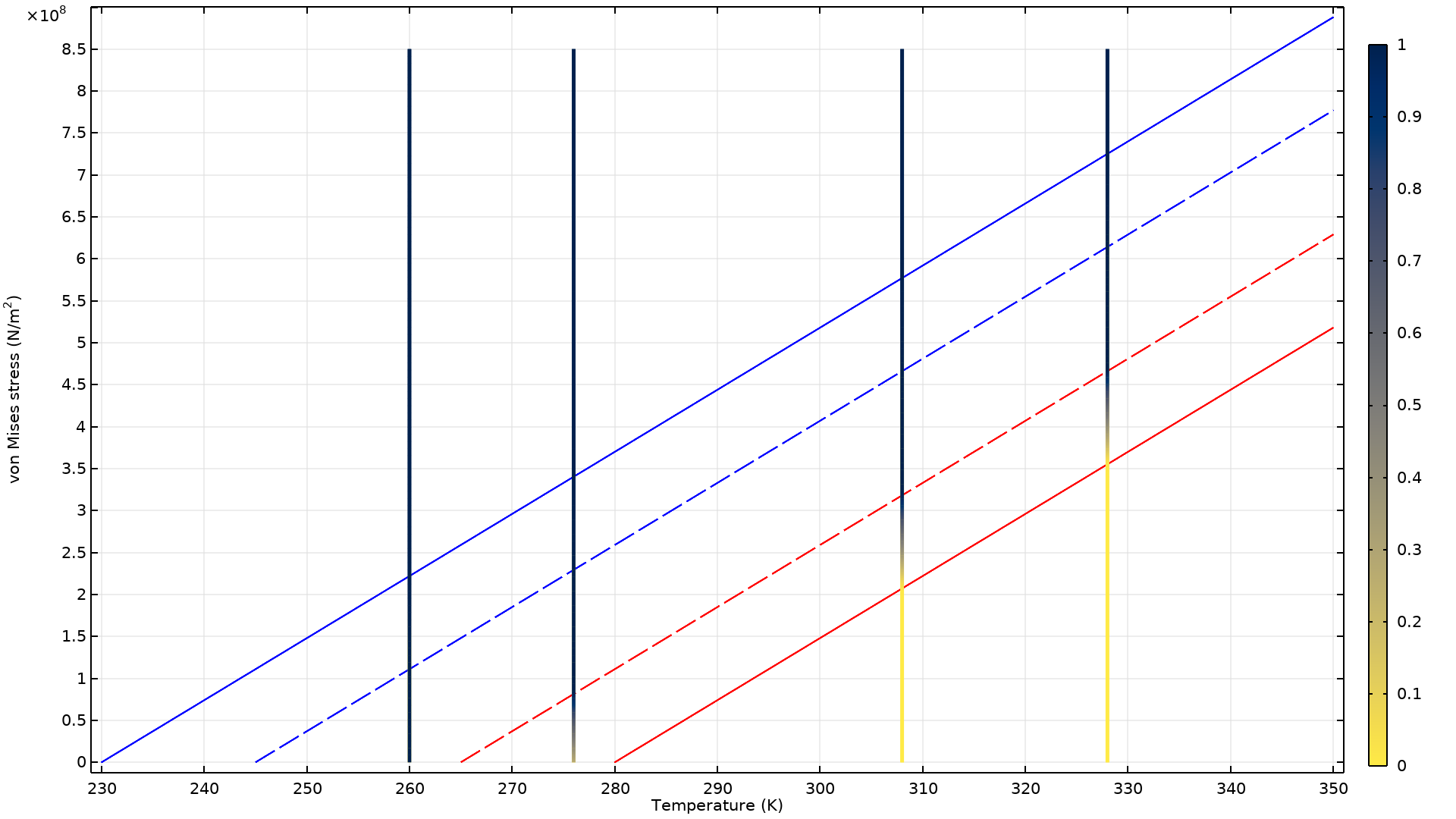
Application Library Title:
uniaxial_loading_of_shape_memory_alloy_souza_auricchio
Download from the Application Gallery
Chloroprene Rubber Compression Test
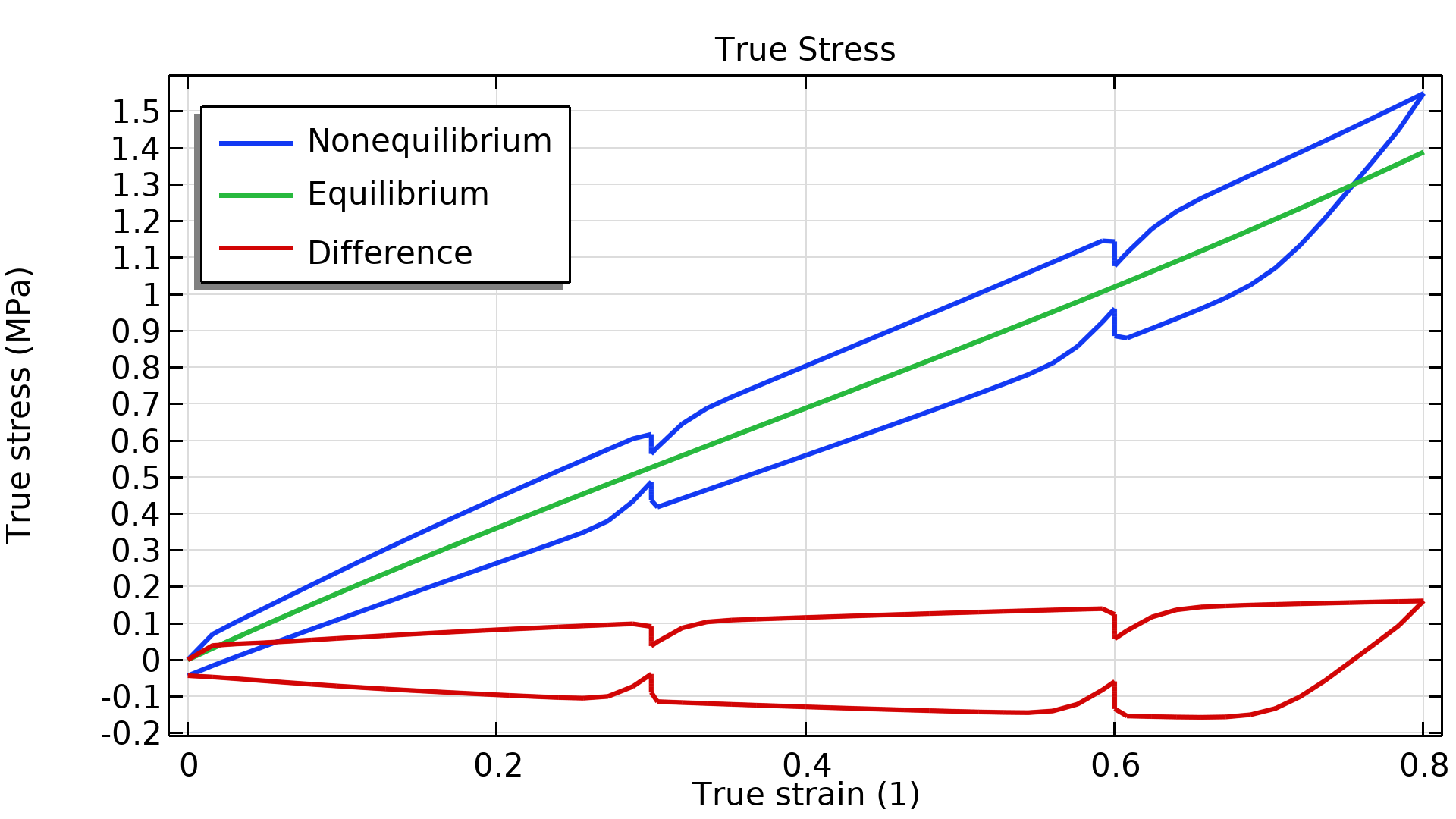
Application Library Title:
chloroprene_rubber_compression_test
Download from the Application Gallery
Buckling of HDPE Liners
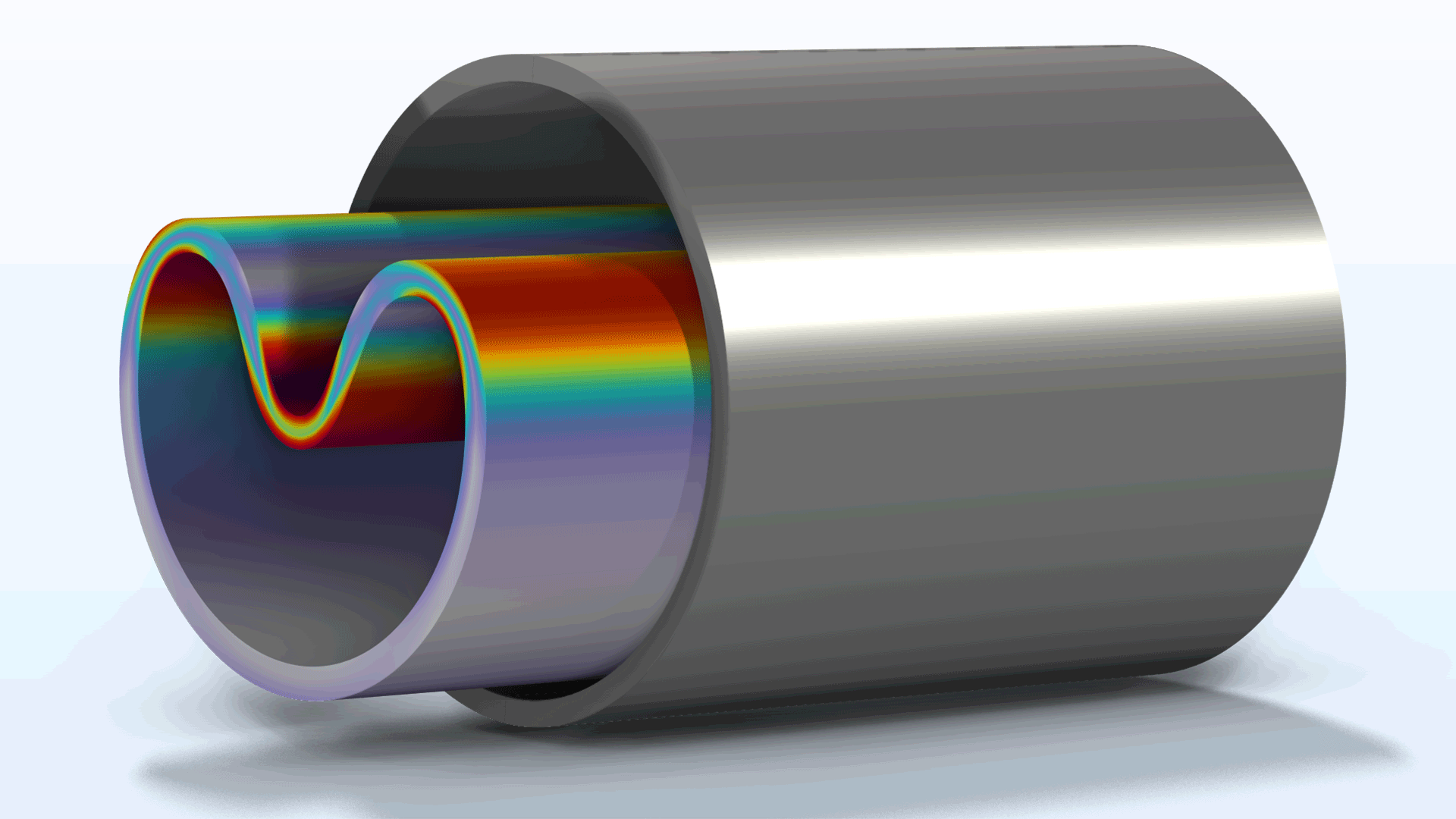
Application Library Title:
buckling_hdpe_liner
Download from the Application Gallery
Uniaxial Stretching of a Rectangular Sheet
Application Library Title:
sheet_uniaxial_stretching
Download from the Application Gallery
Parameter Estimation of Hyperelastic Materials
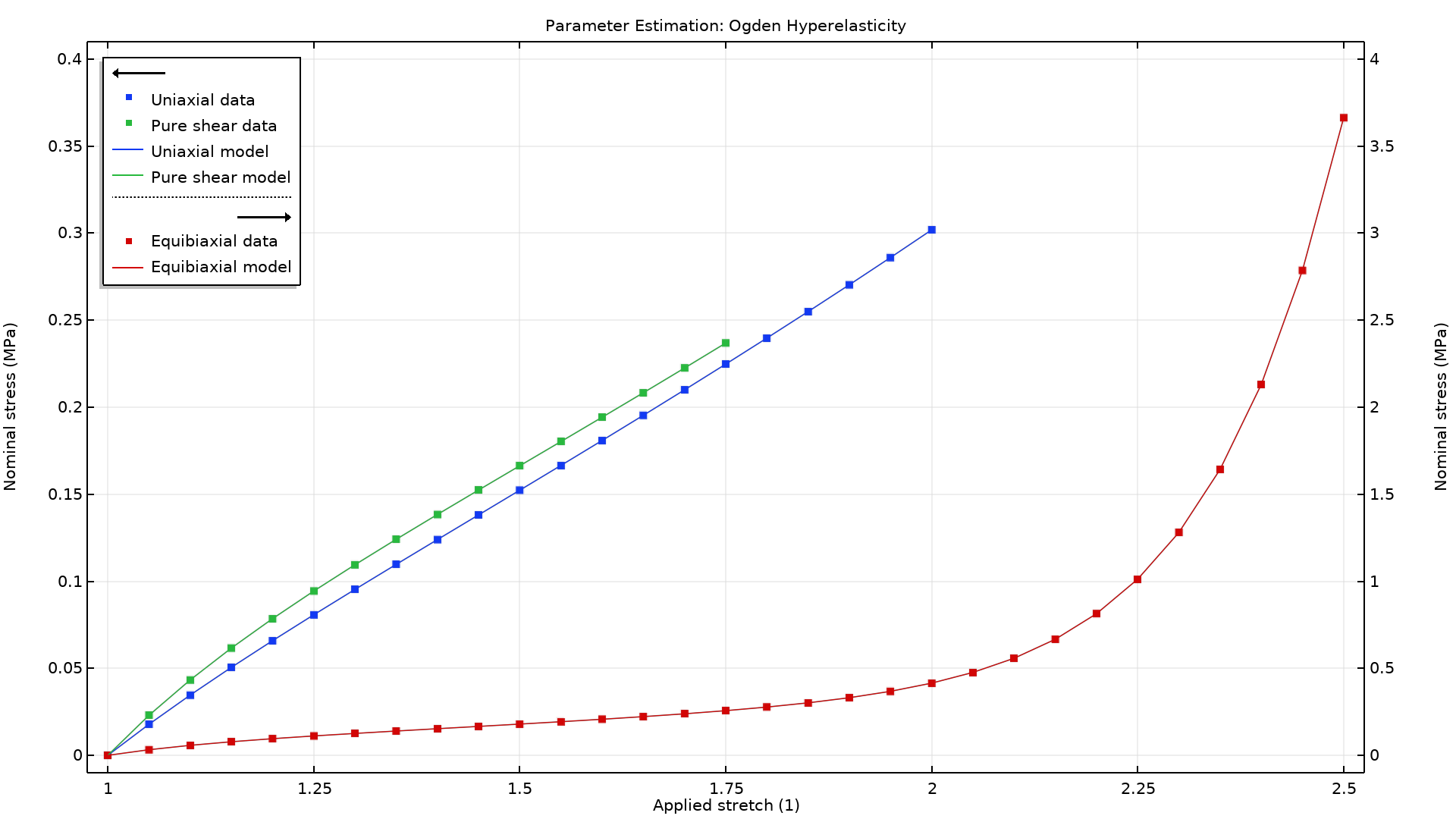
Application Library Title:
parameter_estimation_hyperelasticity
Download from the Application Gallery
Parameter Estimation of Elastoplastic Materials
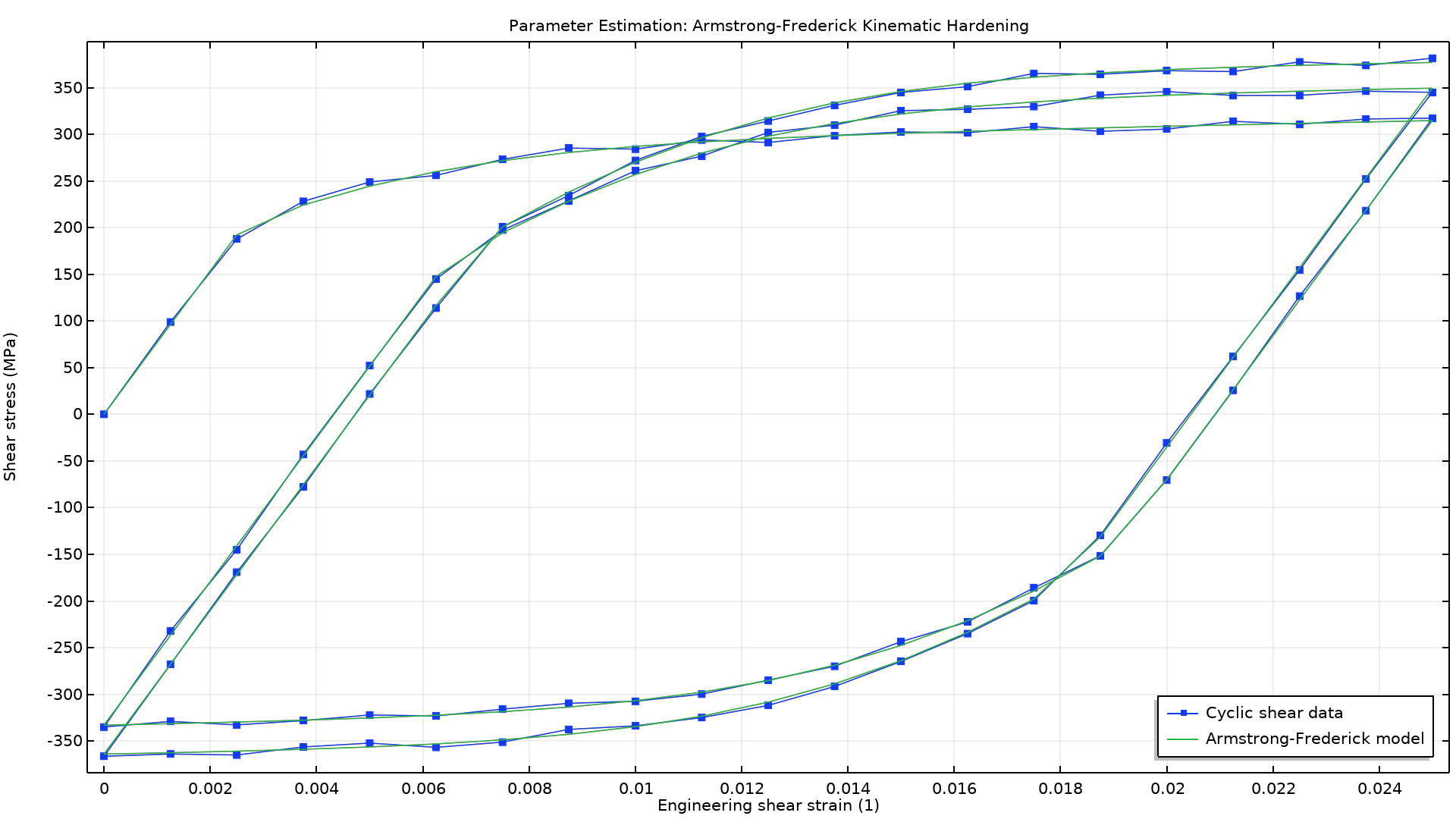
Application Library Title:
parameter_estimation_plasticity
Download from the Application Gallery
Parameter Estimation of Viscoplastic Polymers
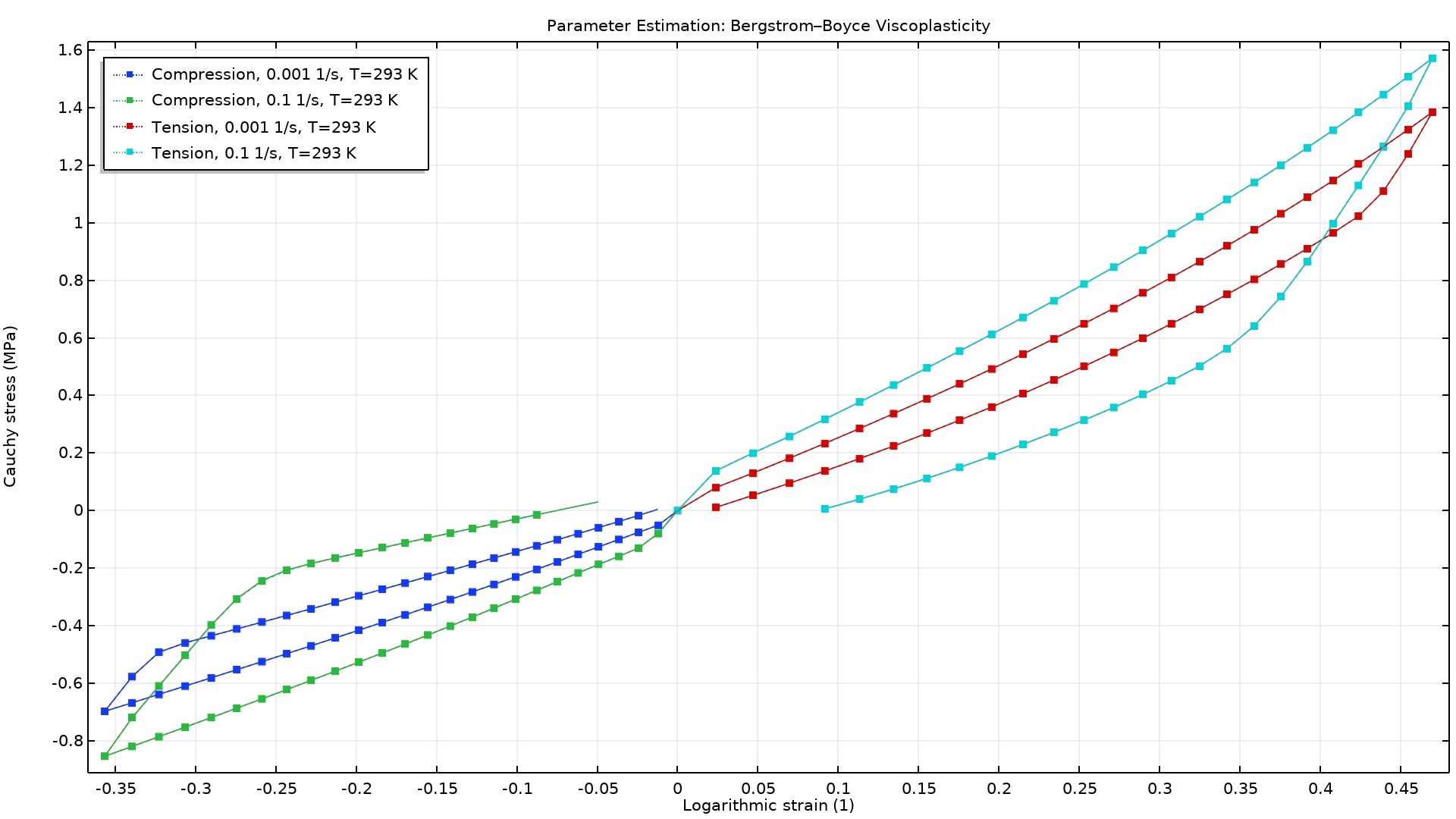
Application Library Title:
parameter_estimation_polymer_viscoplasticity
Download from the Application Gallery
Small Punch Test for Ultrahigh Molecular Weight Polyethylene
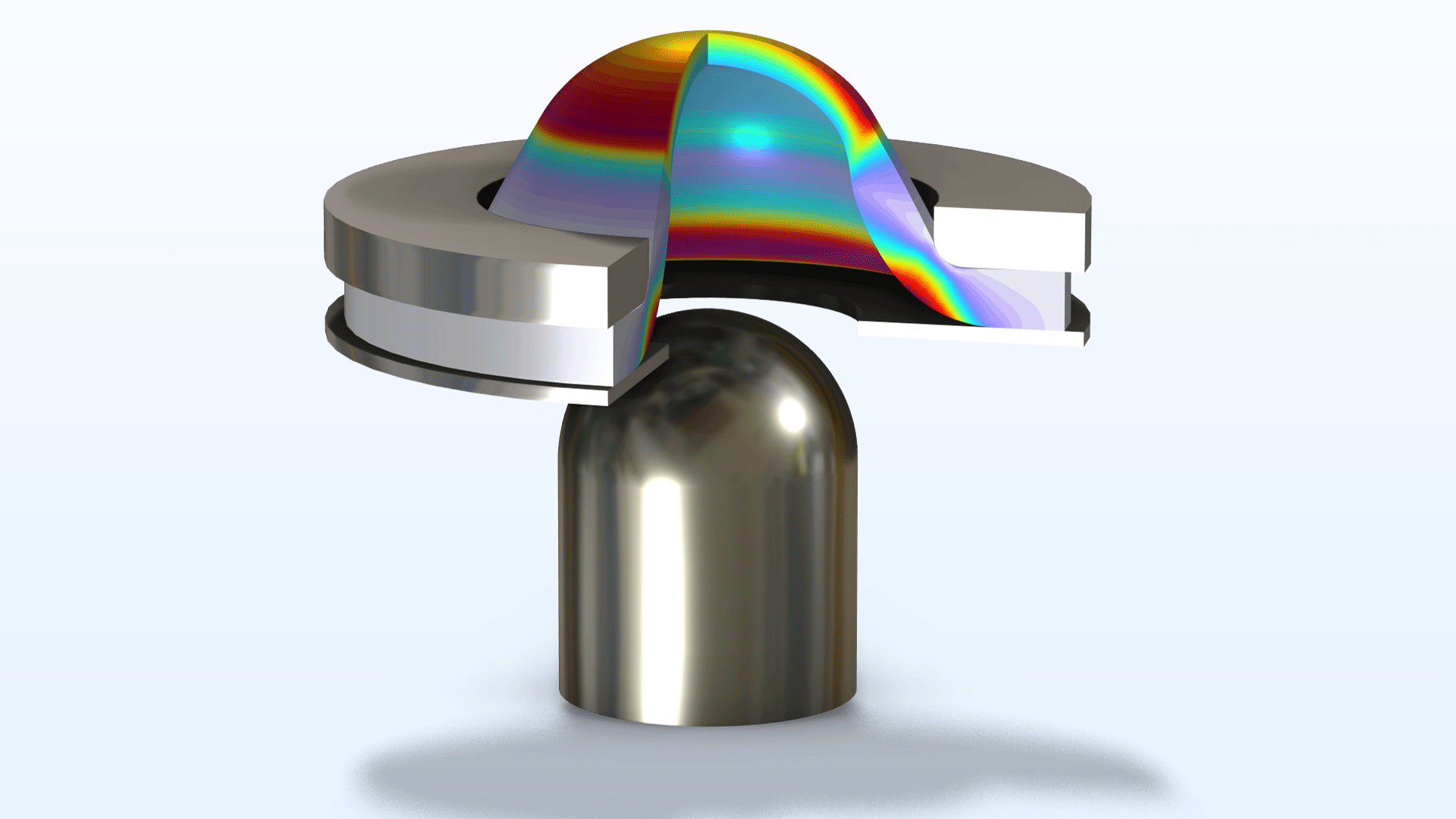
Application Library Title:
small_punch_test
Download from the Application Gallery